Stabilizing Roads and Bridge Abutments with HMI’s Deep Foamjection®
Across the country, transportation infrastructure is under stress—not just from traffic and weather, but from the ground beneath. Settlement, voids, and unstable soils can threaten the integrity of highways, bridge abutments, and roadways long before visible surface damage appears.
At HMI, we specialize in Deep Foamjection®, a process that stabilizes and strengthens weak subsurface soils using high-density structural polyurethane foam. It’s a proven method that’s non-disruptive, cost-effective, and engineered to meet the needs of DOTs and contractors working under pressure.
Common Causes of Road and Bridge Subsurface Issues
Many of the problems DOTs and contractors face stem from complex subsurface conditions, including:
- Water infiltration leading to erosion or washouts
- Poorly compacted fill from initial construction
- Organic or loose native soils that can’t support modern loads
- Void formation from leaking culverts or old utility corridors
- Bridge approach settlement due to differential movement
- Slope instability, especially near embankments or over soft clays
These problems often manifest as cracking, settlement, rutting, or constant maintenance needs. Traditional repair methods—grinding, patching, or adding fill—don’t address the root cause and lead to repeat failures.
Why HMI’s Deep Foamjection® Works
HMI’s Deep Foamjection® process delivers structural support where it’s needed most:
- Injects foam to various depths, depending on soil profile
- Fills voids and blocks off water infiltration paths
- Expands to compact and strengthen weak soils
- Can be designed and verified with DCP and other testing methods
- Installs quickly with minimal surface disruption
It’s a method that fits into tight construction schedules, allows traffic to remain open, and provides an engineered solution that DOTs and contractors can trust.
Ready to Solve the Root Problem?
If you’re dealing with a problematic roadway, bridge abutment, or unstable slope, we’d be glad to discuss how HMI’s Deep Foamjection® can support your next project—literally.
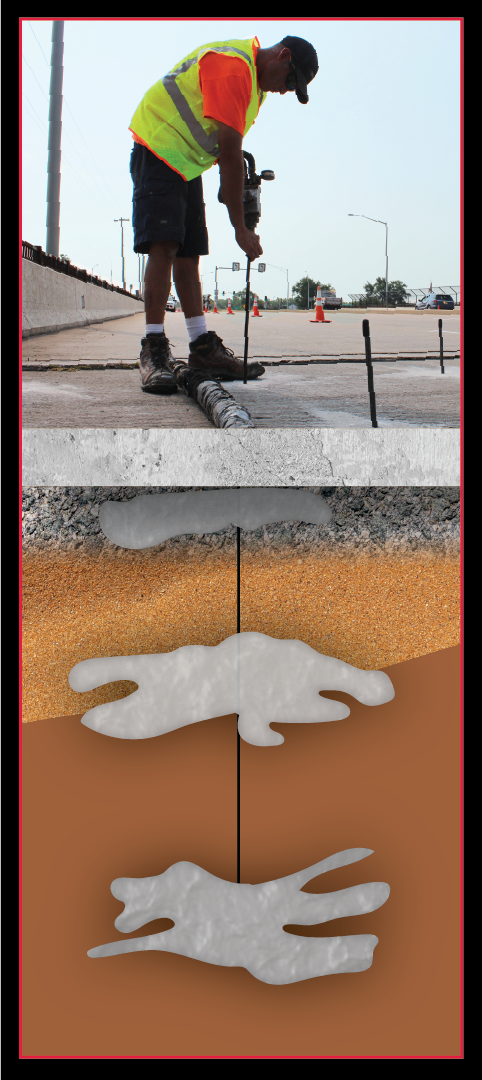
See it in Action:
Case Study: Highway 1 – Fast, Engineered Stabilization for an Active Corridor
A section of Highway 1 in California had developed uneven pavement, cracks, and significant water infiltration. After engineers tested the roadbed, they discovered that there was poor soil compaction ranging 3–12 feet under the highway.
Working in partnership with a local contractor, HMI was brought in to help implement Deep Foamjection®. Using pre-determined injection points spaced every 3 feet and reaching depths of 12 feet, the team injected expanding foam to:
- Densify and strengthen the weak subgrade
- Seal off water pathways contributing to erosion
- Create a more uniform support system beneath the highway
This entire operation was conducted one lane at a time, and the stabilization was completed without any excavation—minimizing downtime and eliminating the need for traditional removal and replacement. The engineers reported significant improvement in surface stability, and the road was successfully resurfaced to significantly extend its life.
Read the full Highway 1 Case Study
Case Study: Bridge Abutment Lift – Burnaby, BC
In Burnaby, British Columbia, a bridge approach slab had settled over several years, creating a dangerous transition. The slope became so steep it caused vehicles to “jump” at the hinge point between the slab and the bridge deck—posing safety concerns and structural stress.
HMI was consulted to lift the slab using Deep Foamjection®. Through incremental injections beneath the abutment, the contractor lifted the slab a full 5 inches, restoring a smooth, continuous grade. The work was performed without excavation or full closure—a significant cost and time savings compared to replacement.
Read the full Bridge Lift Case Study
Field Example: Slope Instability and Deep Voids
In another recent project, slope movement and poor subsurface conditions caused a rural highway to settle repeatedly. Despite years of repaving—up to 3 feet of asphalt in some sections—voids and weak soils beneath remained unaddressed.
HMI’s geotechnical engineer and field team conducted a Dynamic Cone Penetrometer (DCP) test on-site, confirming extremely low resistance from 3 to 10 feet deep. The project was executed using a single-pipe injection method with precise control. Post-treatment testing showed a 140% improvement in soil strength. The success of the DCP-verified solution gave the client confidence in both performance and documentation.