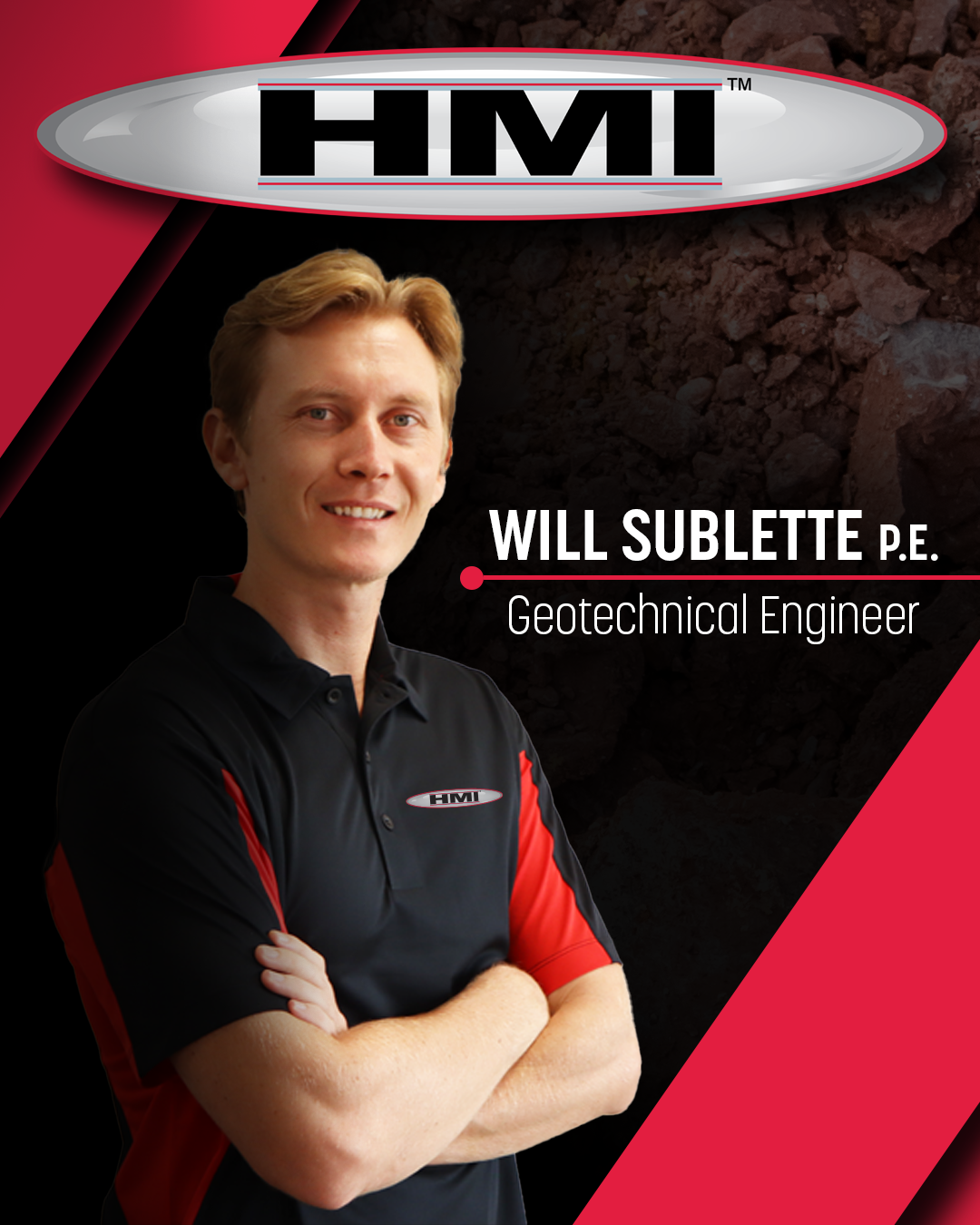
The “Newest” HMI Difference – Introducing Next level Engineering Support
Paul DelFino With this blog, HMI wants to introduce you to Will Sublette, P.E., HMI’s
Home » Blog
Paul DelFino With this blog, HMI wants to introduce you to Will Sublette, P.E., HMI’s
Dive into Excellence: HMI’s Polyurethane Solution for Concrete Pool Deck Repair Concrete pool decks, exposed
Revolutionizing Concrete Garage Floor Repair: HMI’s Polyurethane Excellence for Residential and Commercial Spaces Concrete garage
Revolutionizing Concrete Sidewalk Repair: HMI’s Polyurethane Solution for Residential and Commercial Spaces Concrete sidewalks are
Elevating Concrete Driveway Repairs: The Polyurethane Solution In the realm of concrete driveway repairs, a
Concrete settling and sinking is quite common. It occurs when the soil, at the time
This site is protected by reCAPTCHA and the
Google Privacy Policy and Terms of Services apply.
In 2 days, we teach you everything you need to know to start your own concrete raising company!
We make the most innovative, environmentally responsible poly product on the market, and we do it right here in the U.S.A.